Providing critical oxygen delivery system to Dragon’s Heart Hospital
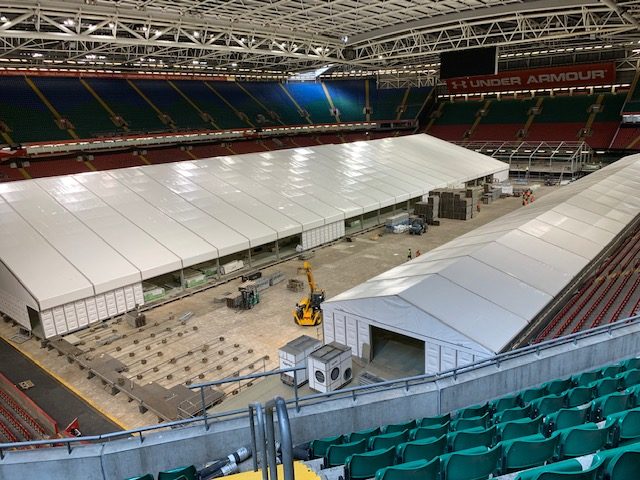
CASE STUDY : ALBUMEDIX LTD Project: Dragon’s Heart Hospital Principality Stadium Client: N G Bailey / Cardiff & Vale University Health Board Timing: April 2020 Value: £1.6M Without oxygen the Dragon’s Heart Hospital, conceived as a response to the coronavirus pandemic, could not function. Demonstrating outstanding commitment, the Medical Gases’ team designed, delivered and installed […]
Critical oxygen system for Royal London coronavirus wards delivered in 21 days
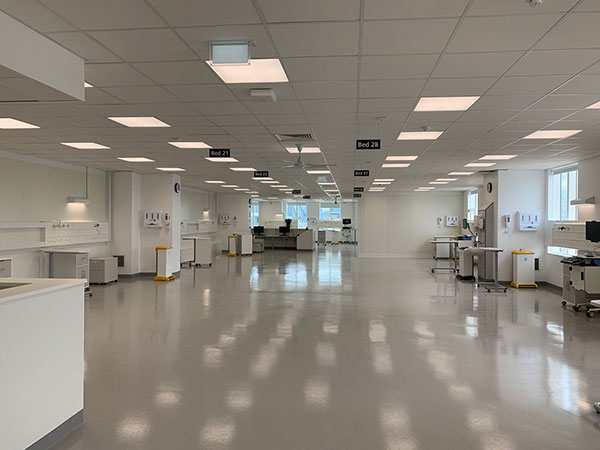
CASE STUDY : Royal London Hospital Project: Royal London Hospital Coronavirus Wards Client: Barts Health Hospital Trust Timing: April 2020 Value: £0.9M Medical Gases worked around the clock to provide the essential oxygen delivery systems to two floors at Royal London, providing capacity for coronavirus patients to relieve the pressure on other hospital facilities […]
Providing essential oxygen systems for emergency COVID-19 Intensive Care facilities
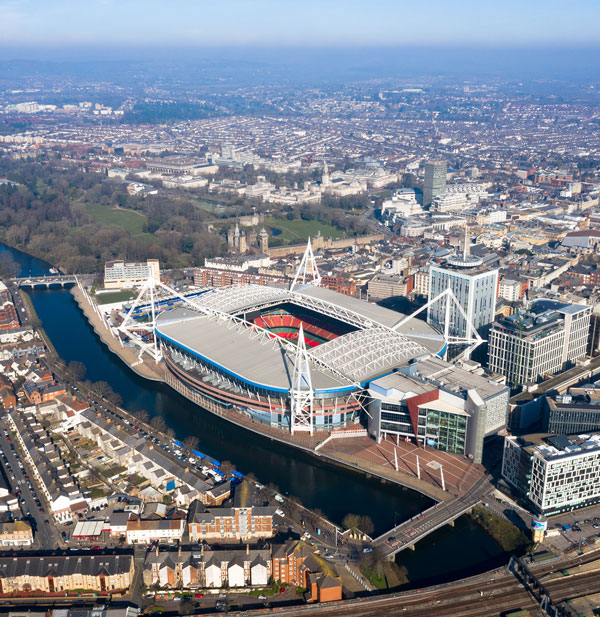
We are immensely proud of our team who worked around the clock at the start of the COVID-19 shutdown to deliver essential oxygen systems for three emergency COVID-19 Intensive Care facilities in London and Cardiff. Our dedicated teams demonstrated their commitment in extremely challenging circumstances delivering new facilities at The Royal London, Epsom General and […]