Delivering Plessey Semiconductors Ltd complex facility upgrade to an aggressive schedule
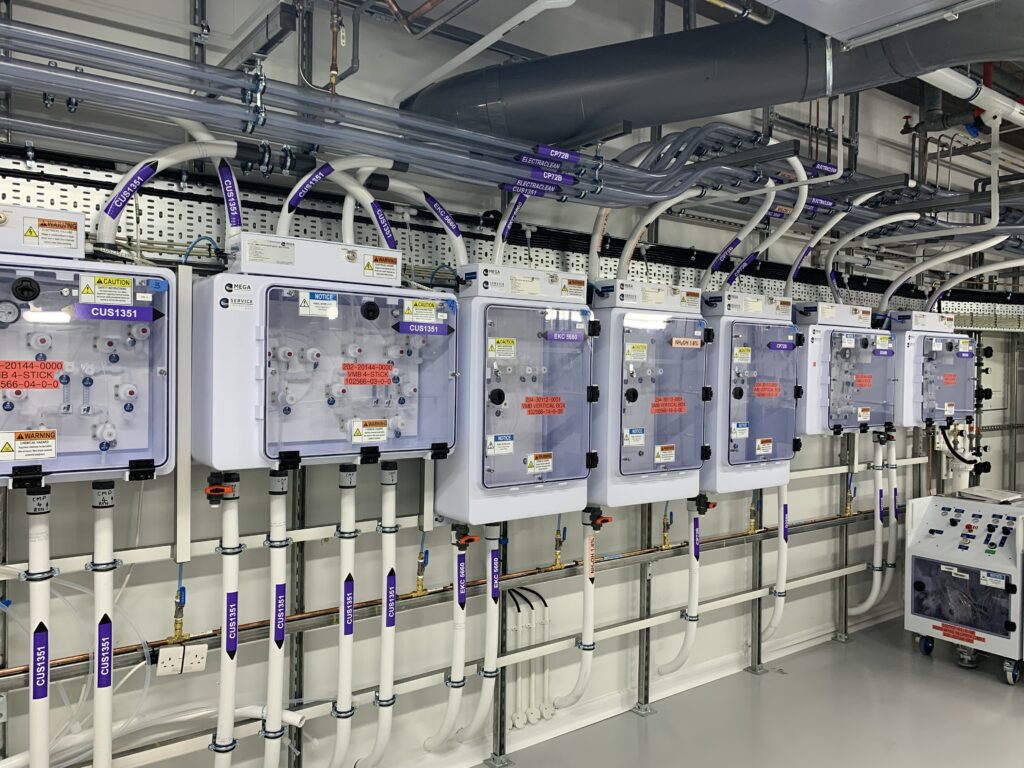
Delivering Plessey Semiconductors Ltd Complex Facility Upgrade to an Aggressive Schedule
Pyrogen free water for the manufacture of vital pharmaceutical ingredients
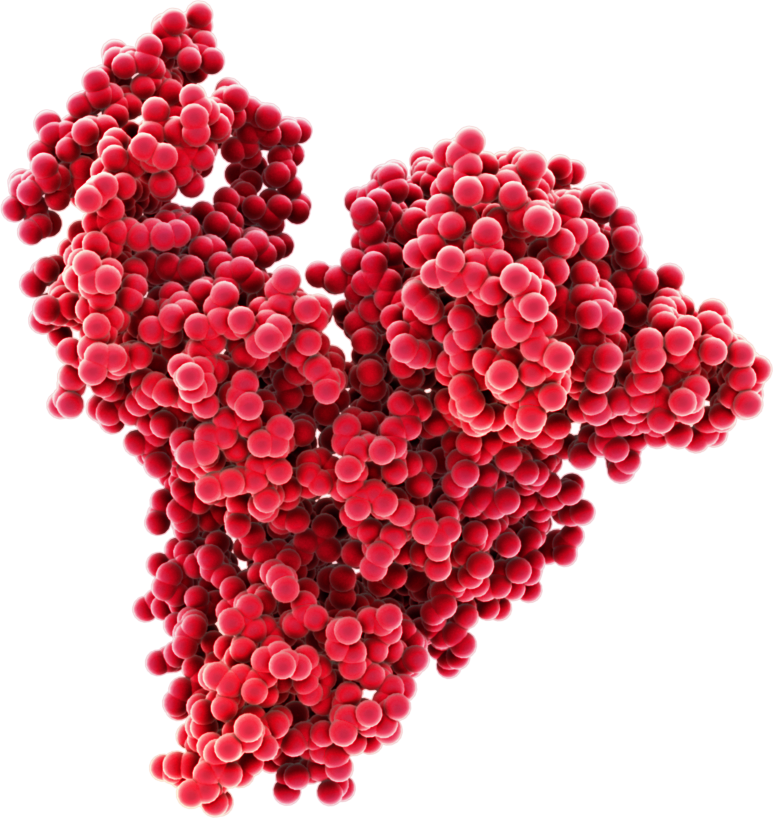
Puretech designed, manufactured, installed and commissioned a fully validated system for the generation and distribution of essential pyrogen free water to replace the existing legacy system at Albumedix’s facility in Nottingham, UK.
Delivering in record time for coronavirus wards at Epsom University Hospital
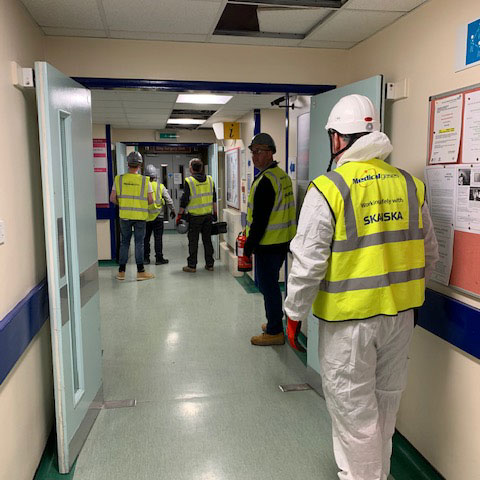
CASE STUDY : EPSOM UNIVERSITY HOSPITAL Project: Epsom University Hospitals Covid-19 Wards Client: Interserve / Epsom and St Helier University Hospitals Timing: 25th – 28th March 2020 Value: £1.6M Medical Gases completed a project, including over 1000 meters of pipework, in less than a week to boost oxygen supplies to the coronavirus wards at […]