Pipework System Design, Fabrication & Installation
We design, manufacture and install pipework systems.
Sectors
- Hospitals,
- Pharmaceutical,
- Biopharma,
- Life Sciences
- Laboratories,
- MOD Facilities
- Data Centres
- Emerging sectors such as Green Hydrogen, SMR (Nuclear) and battery filling/Gigafactories.
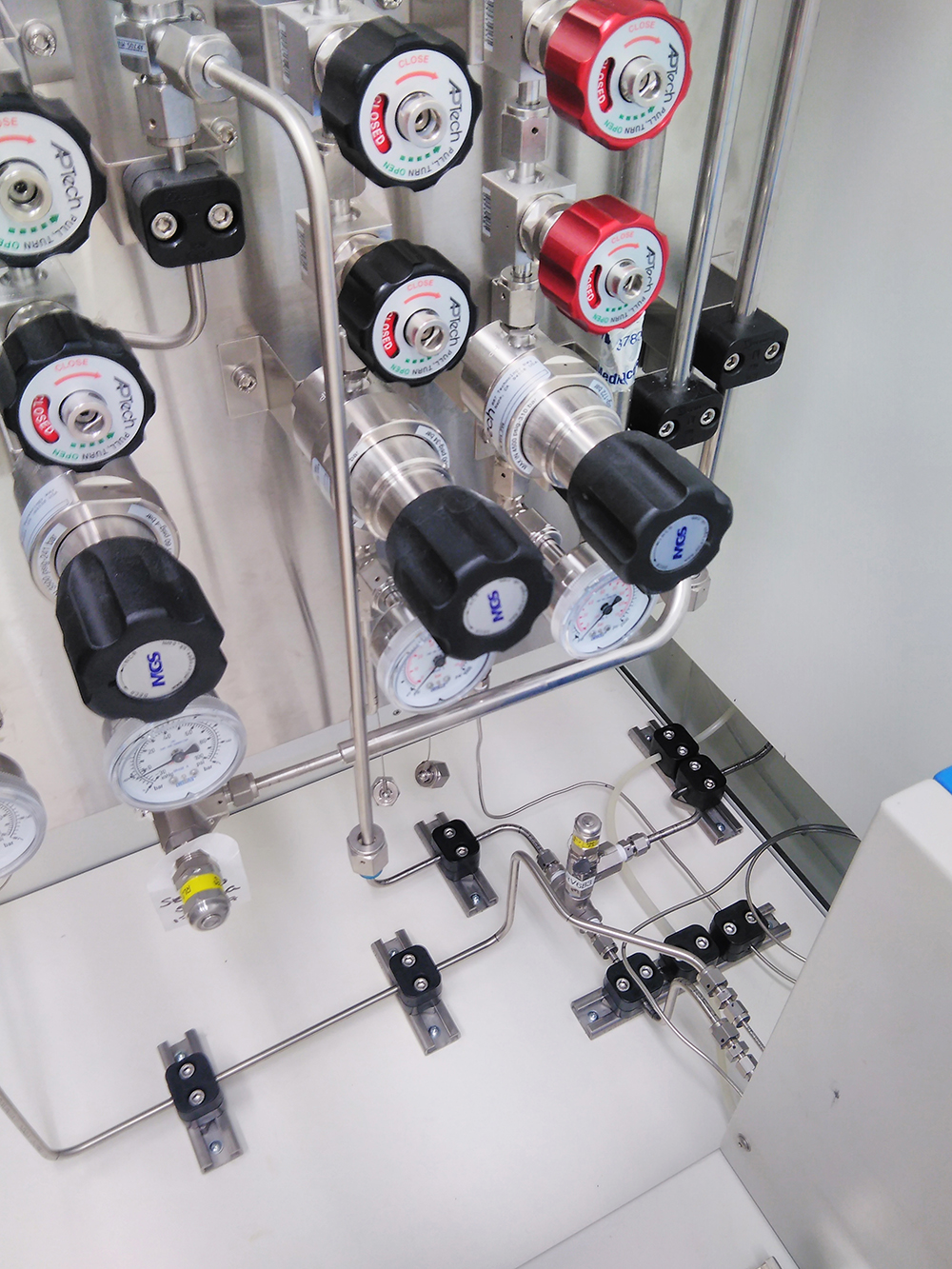
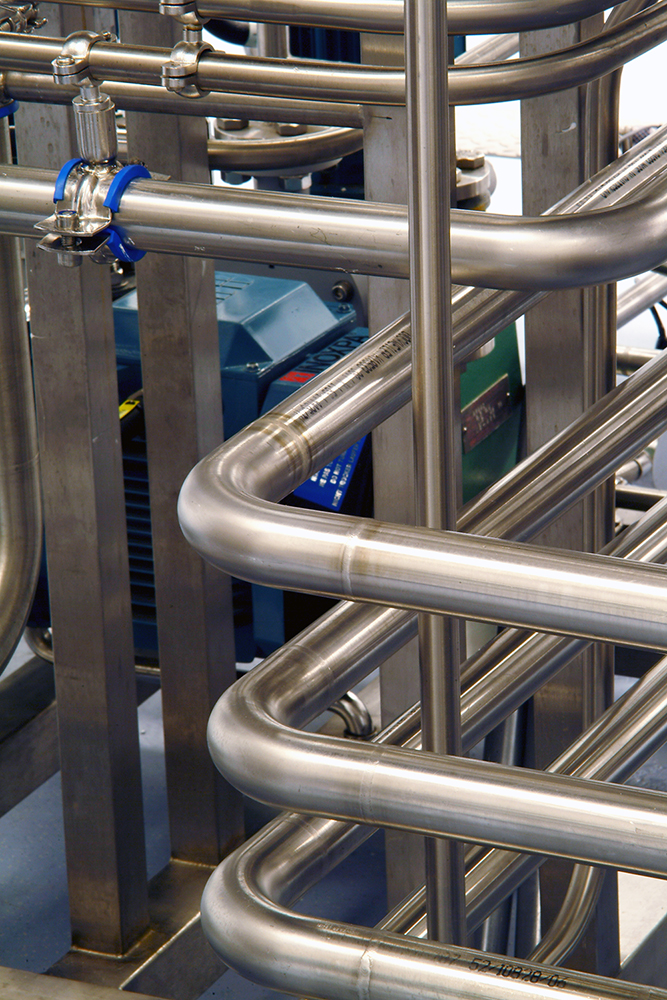
At Puretech, we design and install high-quality, validated pipework systems for Medical Gases, Laboratory Gases, Purified Water, Pure Steam, Vacuum, MRI Quench systems and many more.
With over 40 years of experience, our in-house team manage everything from concept design to commissioning and handover, ensuring full compliance with relevant regulatory body standards. We’re trusted by leading and healthcare, life science, pharma and many more key sector organisations to deliver reliable and compliant pipework installations for critical environments.
Pipework Materials & Sizes:
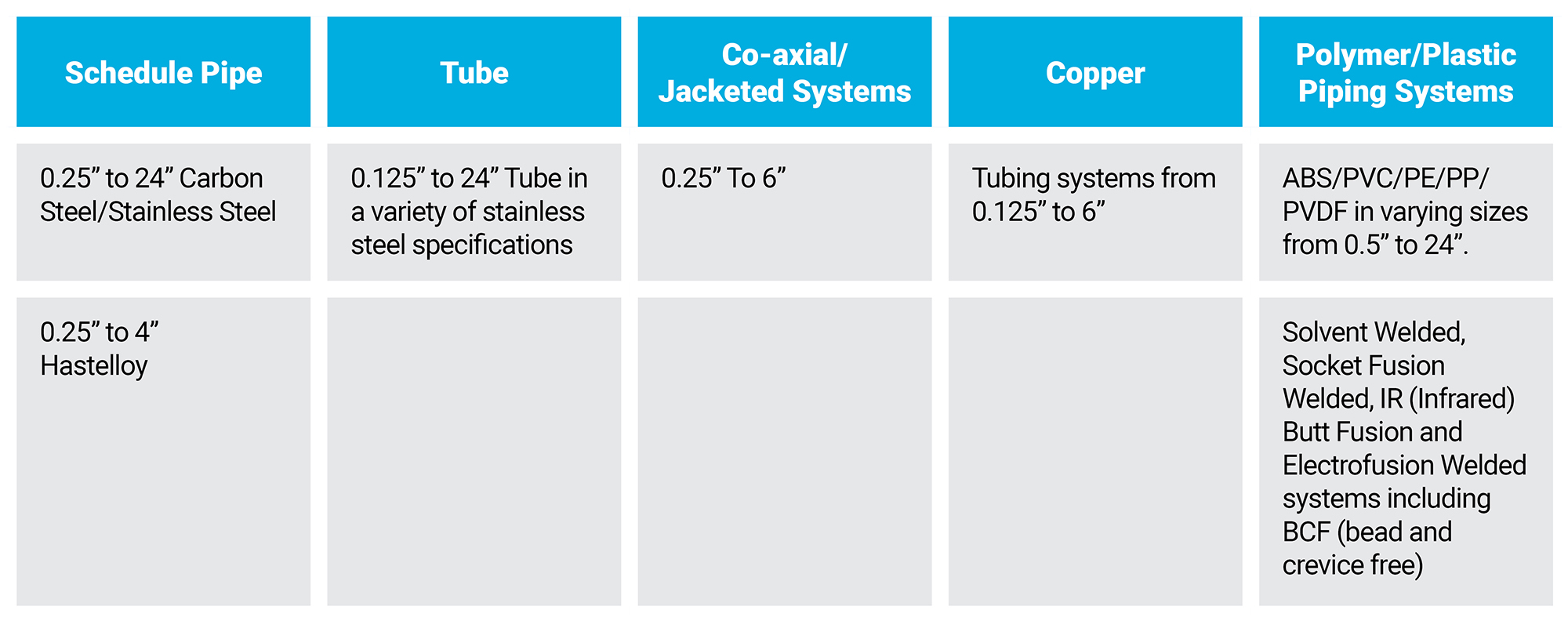
Orbital Welding
Unsurpassed Ability. Uncompromising Quality.
At Puretech, we set the standard when it comes to high purity orbital welding and pipework system installations. We’ve heavily invested in new technology and ensured each weld that comes out is the best quality it can be.
- Highest Quality Standards: We maintain rigorous quality controls, achieving 3.1b certification and ensuring all parts conform to the most stringent specifications before welding begins.
- Advanced Pipe Preparation: Our facing tools ensure that pipe ends are perfectly square with zero deviation, ensuring full weld penetration and structural integrity.
- Certified & Experienced Welders: Our team consists of ASME coded, highly experienced welders operating to ASME IX and other relevant global standards.
- Daily Weld Testing & Total Traceability: Before the start of each working day, our welders test and prepare a sample to guarantee accuracy. Every weld is then recorded in our Engineering Data Book, recording vital information such as pipe & fitting details, weld location (using Isometric drawings), welding operative and certification numbers for total traceability.
Infrared (IR) fusion welding
Perfect for high-purity applications
This non-contact form of welding, which uses infrared radiation to heat and melt parts made from thermoplastics such as Polypropylene and PVDF, makes it perfect for high-purity piping systems where contamination is a concern.
Coaxial Tube in Tube Piping
Absolute Containment
For an added degree of safety in dangerous gases, a COAX tube and fitting is used. This is a double-walled tube system which consists of an inner process tube and an external safety tube allowing for gas leakage monitoring and alertion.
Service Capabilities
Puretech understands how crucial your pipework systems are to your business and clients, from their reliability to ensure continuous manufacturing and the quality of the end product or service, to system compliance ensuring all regulatory body standards are met.
Our service contracts are tailored to our clients’ individual needs and the service is expertly provided through our network of experienced and qualified engineers. We can offer contracts of 1-5 years with the numbers of visits specified by you. All of our contracts as standard receive 24/7 telephone support, recommended spare parts list and a detailed service report to ensure you comply with all regulatory body standards.