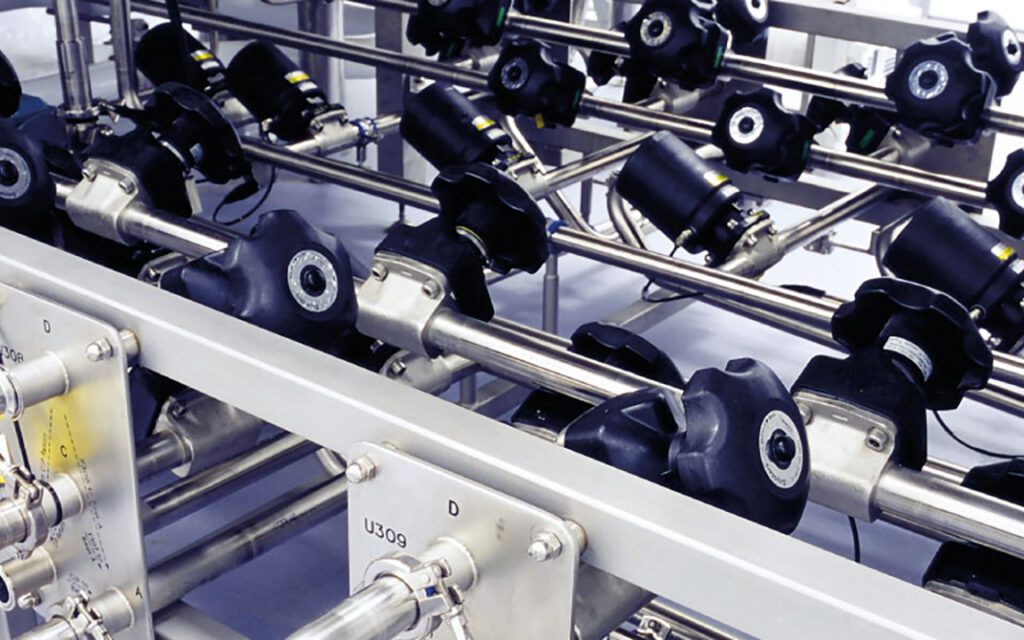
CASE STUDY : B BRAUN
Purified water is an essential ingredient in intravenous saline solution, which is one of the products produced by medical technology company B Braun. Puretech was commissioned to provide a single source solution for the essential clean utilities, including this purified water, water for injection, steam and compressed air, at the company’s new world-class production facility in Malaysia. Puretech worked with B Braun from design to validation to provide the required systems.
Background
B Braun is one of the world’s largest medical technology companies. Over a period of nine years the company has expanded its facilities in Penang, Malaysia with a project encompassing five new and enhanced production plants and other administrative buildings. The result is a state-of-the art facility featuring the latest building and production technologies for the manufacture medical devices for infusion therapy, pharmaceutical solutions and surgical instruments for the treatment of patients in Malaysia and around the world.
The project
Project summary
The design, manufacture, co-ordination, supply, installation, testing and commissioning and validation of turnkey high integrity delivery systems:
- Purified water (PW) generation (Genesys)
- Purified water (PW) storage and distribution
- Water for injection (WFI) generation
- Water for injection (WFI) storage and distribution
- Pure steam generation and distribution
- Clean compressed air distribution (CDA)
Detailed design study to meet exacting specification
Initially, Puretech was contracted to carry out a detailed design study to meet the specifications set out for B Braun’s planned new production facility at Bayan Lepas, Panang, Malaysia.
Co-ordinating with other contractors, Puretech provided detailed process piping and instrumentation diagrams (P&IDs), schedules, general arrangement (GA) drawings and 3D modelling of the entire clean utilities building.
Design to validation
Each system was fully designed and engineered at Puretech’s facility in Surrey, including the controls system integration into the client’s process control system.
All of the site piping, including the process connections to the client’s equipment and process vessels, was undertaken on site by Puretech. Individual skids for the PW systems and WFI system were built at Puretech in the UK and shipped to Malaysia for installation into the new clean utilities building.
All piping systems were fully validated, including site installation qualification, operation qualification (IQ/OQ) and full engineering data books to support the complete installation.
Meeting the challenges
Puretech supplies systems throughout the world and, through experience, has learnt to adapt to the challenges of a variety of climates and to be flexible and innovative in carrying out installations where the availability of general consumables and infrastructure parts is limited, as was the case for this project. Welding plant, tools and equipment of the quality required were also not readily available locally for this project and the climate and logistics of an overseas installation were compounded by a scarcity of appropriately qualified people locally.
Puretech Project Manager, Ian Chapman lived in Malaysia for 18 months to be on-site and to overcome any issues, ensuring successful delivery. Puretech worked to a tight programme for the production plant to be available and in service ready for commissioning. The total project from initial discussion took around three and a half years, with the installation and site works taking less than 15 months of this, including commissioning and validation. For the passivation acid rinse of the pipework Puretech sent out its own passivation kit and expert and bought citric acid locally.
The sheer scale of this project, which is one of the largest LVP (large volume parenteral) installations in Asia, was a step change for Puretech. Typically, systems contain 10 000 litres, the installation at B Braun contains 100 000 litres of WFI split into two 50 000 litre vessels.
“We are very proud of our delivery of this significant project, working in challenging conditions and to a tight programme. The client was very impressed with the quality of our work”
Robert Smith, Sales and Commercial Director
Producing a vital ingredient
The system Puretech has designed for B Braun supplies WFI for LVP and SVP holding intravenous saline solutions for bags. The WFI is a carrier for Braun’s product and a vital ingredient, forming more than 90% of the final product.
A system designed for a facility in a hot climate must be modified accordingly. For B Braun the system feed water is warm, 25° versus circa <15° for European projects, so has to be chilled to 15°c for purified water to reduce microbiological growth. Purified water has to be distributed in insulated piping to maintain this. WFI is maintained at 70 to 80°c.
Safety and sustainability
In terms of safety, throughout the installation and site works Puretech had zero accidents. Puretech is conscious of sustainability in the design and delivery of its systems. In this instance the necessary hardware was packed in wooden crates and shipped in containers. There was very little on site wastage, which is always Puretech’s objective.
Sources: