Water for Injection
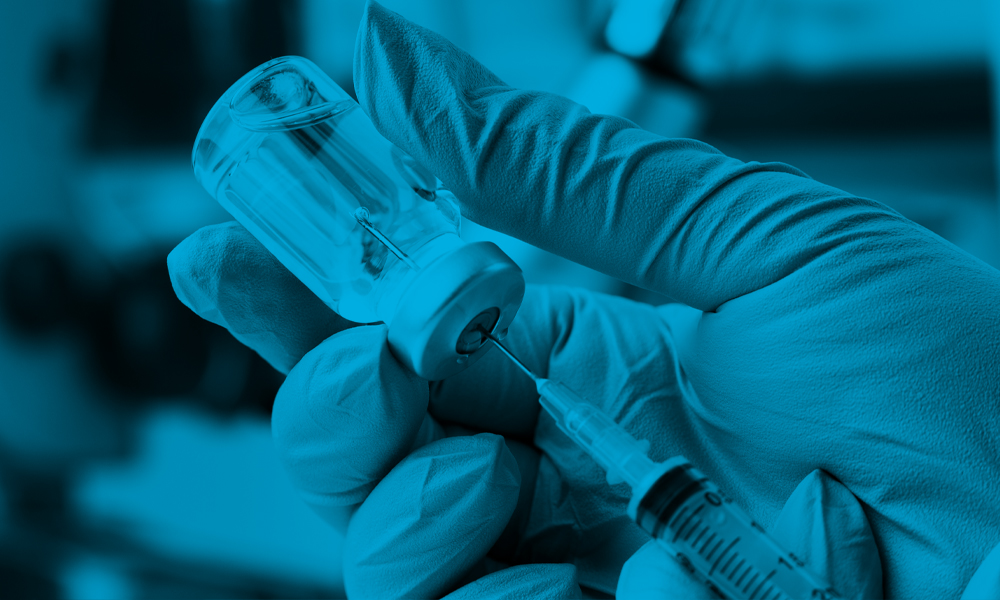
Talk to us
For more information about our solutions why not download our brochures
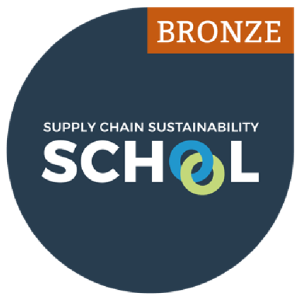
FAQs - Water for Injection
- Is it possible to produce hot water from a membrane system?
No, it is not possible to produce hot water from the technology itself, but the water could be heated once it is in the tank, or even before by adding a heat exchanger between the generation system and the storage tank. - Can an existing purified water (PW) system be converted to a WFI
generation system?
In theory a purified water system can be converted to a WFI generation system from a water quality perspective but in reality there may be issues when it comes to validating the system and ensuring that the regulators are happy that it is producing WFI and not PW. - Where would you recommend installing an online microbial monitor?
Puretech would recommend installing an online microbial monitor at the return end of the distribution loop, before the water goes back into the storage tank. - Are there any situations/processes where you would not recommend the membrane technology?
Not really, EUR Pharmacopeia, US and JP Pharmacopeia all allow membrane technology, but Puretech would recommend checking with your regulator to see whether they would accept membrane technology to obtain WFI, and if they will not it could be considered a risk. - Does regulatory guidelines allow cold WFI distribution ?
Yes. Water temperature is not one of parameters for WFI but certain applications that WFI is used for will require hot water. - Is it necessary to sterilise a membrane WFI generation system, from a regulation point of view (given that WFI is it a sterile media)?
Puretech recommends regular heat sanitisations of generation systems to ensure they deliver the quality of water required, especially from a bacteria perspective. - Is further treatment of WFI required when storing it in a tank?
No further treatment is required for stored WFI, but Puretech recommend that if you are storing it cold to maintain a temp below 20°C. - Is it mandatory to have a second stage RO membrane to produce WFI or just advisable?
Puretech recommends a twin pass secondary membrane but it is not mandatory to produce WFI. - What’s the best sanitisation method for WFI in cold distribution ?
There are three options for the sanitisation of WFI in cold distribution – hot water >80℃, super-heated and ozone – all of which are tried, tested and reliable. There are pros and cons for each one so ultimately the decision will depend on how the water is being used in your facility, down time, costs etc. - Can you advise how to remove the bacterial endotoxin using only membranes?
Puretech would not guarantee meeting the bacterial endotoxin required for WFI without an ultra-filter and regulators would not accept a system without ultra-filtration.
Water for Injection (WFI) is widely used in the pharmaceutical and biotechnology industries, in production but also for washing equipment, vessels etc. WFI is a higher quality than purified water and has it’s own standards set out by the worldwide pharmacopoeias (European Pharmacopoeia, United States Pharmacopoeia, Japanese Pharmacopoeia, etc.).
There are many things to consider when choosing your WFI generation system. Whether the water is to be used hot or cold or a mixture of both? What are the local gas, water and electricity costs? What’s the Capital Expenditure budget?
Puretech has a technology to suit all our clients needs, steam heated Stills or electrically heated Stills, as well as membrane technology systems.
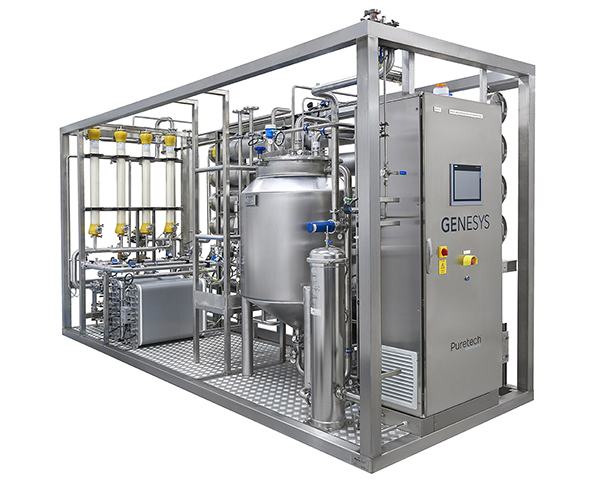
GENESYS WFI (Membrane Technology)
GENESYS is the ultimate water purification system – a thermal sanitisation system that provides a single source solution for taking softened water to Water for Injection quality.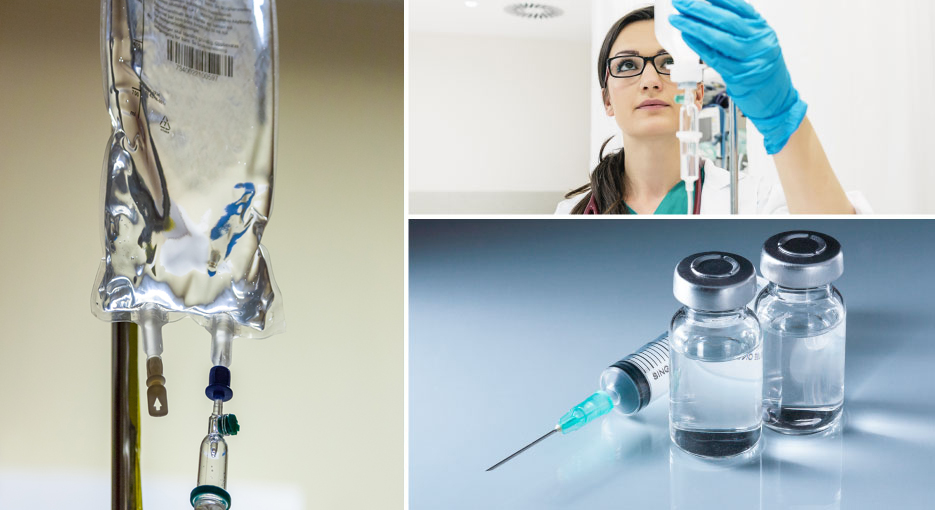
Multi Effect Distillation
Puretech’s Multiple Effect Distillers (MED) are designed and manufactured according to cGMP to produce compendial Water for Injection (WFI). Each unit contains a number of boiling columns (or effects) with the first column producing pure steam, which is condensed and re-distilled in the following columns decreasing the operational costs.
Heating for evaporation and cooling for condensation processes are performed by double tube sheet (DTS) exchangers. Condensation is achieved by means of thin-falling film technology. The process is repeated through each column with the higher number of columns reducing the overall utilities consumption of the system. However, the number of columns does not influence the quality of the product or the capacity of the equipment.
A special labyrinth separator installed at the top of each column which separates the steam generated from any carried over water droplets in the steam itself. The result is a pure, “dry”, pyrogen-free steam, condensed to achieve compendial Water for Injection.
The first column of the Still may be used to produce WFI & Pure Steam alternatively or simultaneously. Pressure vessels are designed according to ASME and PED regulation and the equipment features:
- Double tube sheet heath exchangers
- Certified AISI 316L stainless steel mirror-polished and passivated product contact surfaces
- AISI 304 frame, jackets and control board
- PTFE gaskets
- Pneumatic valves with Teflon membranes and AISI 316 L SS polished body
- ASTM C-795 – compliant insulation.
Capacities range from 50 to 15,000 l/hr with three to ten columns
Vapour Compression Distillation
Puretech’s Vapour Compression Distiller (VCD) is manufactured according to the international cGMP (Good Manufacturing Practices) and Pharmacopoeias. A vapour compression still can potentially work with any feed water; furthermore, customised systems with pre-treatment integrated on the same skid with reverse osmosis and the ability to be electrically heated and steam heated are all standard options.
Puretech’s “thermocompression” still can produce both cold distillate or hot distillate with huge savings on energy costs, when compared to MED, with no need for cooling water. Whether electrically heated or plant steam heated capacities range from 20 to 20,000 l/hr with one or more blowers.
The benefits of Vapour Compression Distillation technology are:
- Low energy consumption
- No need of cooling water to condensate the pure steam
- No need for high quality inlet water (in some cases even softened water can feed the VCD)
- No need to pressurise the inlet water
- WFI outflow at high pressure (1–1.5 bar) without an additional pump requirement
- Safe process, with no risk of any cross contamination through plant steam or inlet water
- Highest flexibility in terms of capacities and WFI temperatures
- Reduced Maintenance
As with all of our distillation systems, the VCD is made in certified AISI 316L stainless steel and all internal parts in contact with the feed water, Pure Steam and the Distillate, are mirror-polished. All hydraulic connections are sanitary tri-clamp or flange connections and gaskets are made from PTFE.
A fully automated Siemens®, Rockwell®, SCADA system, ensures easy operation and complete monitoring of critical parameters. Password restricted access and access history can be managed according to 21 CFR PART 11.
Komb System Multi Effect Still + PS Generator
Our KOMB system is a unique design for the simultaneous production of WFI and PS, combining functions of a Multiple Effect Distiller (MED) and of a Pure Steam Generator (PSG) on a single skid, reducing the space requirements and cost.
A single SCADA system controls both the MED and PSG which is capable of providing separate or simultaneous production of Water for Injection and/or Pure Steam.
Service & Maintenance
Puretech have nearly 30 years’ experience of servicing and maintaining pharmaceutical, validated water systems.
Our service contracts are tailored to our clients individual needs and the service is expertly provided through our network of experienced and qualified engineers.
We can offer contracts of 1-5 years with the numbers of visits specified by you. All of our contracts as standard receive 24/7 telephone support, recommended spare parts list and a detailed service report to ensure you comply with all regulatory body standards.
Let’s Discuss How We Can Work Together!
We would welcome the opportunity to discuss how Puretech can become your trusted partner. We’d love to schedule a meeting to explore potential synergies and discuss how we can support your design projects with our expertise.
Please contact us to schedule a meeting:
- Email: sales@puretech.uk.com
- Phone: +44 (0) 1737 378 000
- Website: www.puretech.uk.com